Industrial Metalworking Techniques
Industrial metalworking techniques refer to the processes and methods used in the large-scale manipulation and shaping of metals for manufacturing and construction. These techniques have evolved significantly since the Industrial Revolution, transforming industries and enabling the mass production of goods.
Overview
The industrialization of metalworking introduced mechanized processes that enhanced efficiency, precision, and scalability. This advancement allowed for the development of complex machinery, infrastructure, and consumer products. Key to this evolution were innovations in processing techniques, machinery, and the understanding of metallurgical properties.
Key Techniques
Several industrial metalworking techniques are employed today, each with specific applications and benefits:
-
Casting: Used extensively in the automotive and aerospace industries, casting involves pouring molten metal into a mold where it solidifies into a desired shape. This technique is ideal for creating large quantities of identical parts, such as engine blocks and turbine blades.
-
Forging: This involves shaping metal using compressive forces, often with hydraulic presses or power hammers. Forging is known for producing components with superior mechanical properties, such as crankshafts and axles, due to the alignment of the metal's grain structure.
-
Welding: A critical process in the assembly of metal structures, welding joins metals by melting the workpieces and adding a filler material. Techniques such as MIG, TIG, and arc welding are common in the construction of ships, buildings, and pipelines.
-
Machining: Encompassing processes like turning, milling, and drilling, machining removes material from a workpiece to achieve precise dimensions. CNC (Computer Numerical Control) machines have revolutionized this field by providing high accuracy and repeatability.
-
Stamping: This involves using a die to cut or shape metal sheets into desired forms. Stamping is widely used in the production of automotive body panels and electronic components, where high volume and consistency are essential.
Technological Advancements
The field of industrial metalworking has seen several technological advancements, particularly in adaptive machining systems and smart foundries. These innovations aim to improve production efficiency, reduce waste, and enhance the quality of the end products.
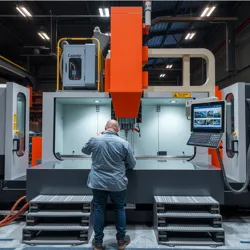
Environmental Considerations
Industrial metalworking processes often have significant environmental impacts, including energy consumption and emissions. The development of eco-friendly foundry practices seeks to address these concerns by minimizing waste and utilizing renewable energy sources. Initiatives such as closed-loop recycling and the use of sustainable materials are also gaining traction within the industry.
Future Prospects
The future of industrial metalworking is likely to be shaped by advances in automation and digitalization. The integration of artificial intelligence in metal fabrication is set to enhance predictive maintenance and process optimization. Moreover, the rise of sustainable alloys promises to reduce the environmental footprint of metalworking.
As these technologies continue to evolve, they will play a crucial role in the ongoing transformation of industries reliant on metalworking, from transportation to construction and beyond.
See Also
- Adaptive Machining Systems
- Smart Foundries
- Eco-friendly Foundry Practices
- Artificial Intelligence in Metal Fabrication
- Sustainable Alloys
References
- "Advancements in Industrial Metalworking," by J. Smith.
- "The Future of Metalworking: Automation and Sustainability," Industrial Review Journal.
- "Innovations in Casting and Forging," by L. Mettal.